Różnica między DC i PLC
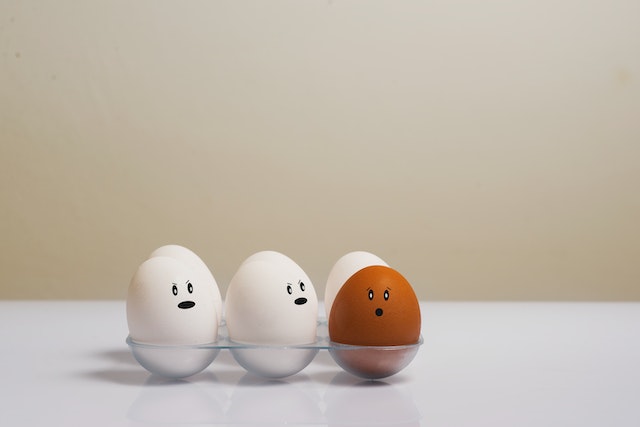
- 3131
- 541
- Klarencjusz Rybak
DCS vs plc
W procesie produkcyjnym istnieją dwa rodzaje kontroli, które można zastosować. Jednym z nich jest zaprogramowany kontroler logiczny, w przeciwnym razie powszechnie określany jako PLC, a drugi to DCS lub system sterowania rozproszonym. Zaprogramowany system kontroli logiki jest samodzielną kontrolą i jest opracowany do wykonania określonego zadania. DCS, z drugiej strony, funkcjonuje jako system sterowania, który może działać na różnych poziomach, aby wynik końcowy został osiągnięty. Oznacza to, że DC mogą być utworzone przez kilka poziomów PLC przy tworzeniu w pełni funkcjonalnego systemu.
Tradycyjnie sformułowanie DCS było niezwykle drogie i było zalecane tylko dla przetwarzania partii, ponieważ mieli różne poziomy produkcji przed dostarczeniem produktu końcowego. Ta koncepcja odbywa się dzisiaj, choć z kilkoma zmianami, które miały miejsce po drodze.
Wiele rozwiązań PLC i DCS zostało opracowanych w czasie, aby ułatwić automatyzację i całe procesy kontrolne. Jedno z opracowanych rozwiązań PLC zostało połączone z HMI (interfejs ludzkiego maszyny)/SCADA (kontrola nadzorcza i akwizycja danych), która umożliwia interakcję użytkownika. Ponadto PLC jest narzędziem zarządzania, które ma dość analogiczną funkcję sterowania do zarządzania procesami. PLC zapewnia utrzymanie logiki drabiny. Jest to preferowane rozwiązanie do użytku dla producenta oryginalnego sprzętu (OEM) i specjalnych potrzeb projektowych. W przypadku interakcji użytkownika należy zapewnić panele HMI/SCADA.
W przypadku nieco większych procesów preferowane jest DCS. Pozwala to na łatwiejsze zarządzanie procesami, które są poza zakresem zarządzania pojedynczym PLC. Małe zarządzanie DCS jest znacznie lepsze w porównaniu z tradycyjnymi systemami zarządzania DCS, głównie z powodu mniejszego śladu. Również system ma bazę danych diagnostycznych, która obniża koszty własności.
W przypadku dużych procesów zaleca się duże rozwiązanie DCS. Jest to kontrola rozproszona, która ma wiele funkcji, które pomogą w spełnieniu wymagań produkcyjnych. Funkcje takie jak zbieranie kontroli wyjściowych, alarmujące, przetwarzanie i gromadzenie danych wszystkie są zarządzane w systemie DCS. Istnieją określone miary wprowadzone w rozwiązaniu DCS w celu obsługi każdego procesu. Z całym systemem zsynchronizowanym żadna awaria pojedynczego systemu nie może prowadzić do awarii innego systemu innej części.
Rozkład geograficzny obszaru jest również czynnikiem przy podejmowaniu decyzji między PLC i DCS. Jeśli funkcje kontrolne zostały rozłożone w różnych lokalizacjach geograficznych, można wziąć pod uwagę użycie PLC lub nawet DC, w zależności od potrzeb. Posiadanie różnych procesów indywidualnie może pomóc w pojedynczej części systemu w jego zarządzaniu, zwłaszcza gdy powstaje awaria, ponieważ awaria danego systemu nie oznacza, że cały proces powinien się zatrzymać szlifowanie.
Algorytmy kontrolne w DCS powinny być rozwinięte, ponieważ pętla między zmierzonym i manipulowanym wejściem obsługuje cały proces. Kiedy słowo „system” jest wymienione w DCS, oznacza to, że jeden proces jest powiązany z resztą i istnieją różne procesy fizyczne rozłożone na szerokim obszarze. Aby upewnić się, że kontrola PLC działa zgodnie z oczekiwaniami, w PLC powinny odbywać się dwa procesy, jedno kontrolujące dany proces, podczas gdy drugi chroni proces. Mniejsze PLC mogą mieć ten sam jednostka z procesami sterowania i zabezpieczającym.
Streszczenie
PLC jest używany głównie jako kontroler procesów i jest głównie samodzielnym programem.
DCS jest używany głównie jako system sterowania i będzie zawierał różne procesy, które mogą składać się ze połączonych PLC.
Zarówno DCS, jak i PLC można skonfigurować lub ponownie skonfigurować.
DCS jest stosunkowo dużym systemem, podczas gdy PLC jest małym systemem.